Kilka lat temu kupiłem w IKEA rozkładane łóżko dla córki. Chciałem kupić teraz identyczne, ale już takiego samego nie ma. Jest za to nowa wersja, która dla użytkownika różni się nieznacznie, ale jest też o 25% lżejsza, ma mniej części, dużo mniej zaczepów materaca, a funkcjonalność wcale nie jest gorsza. W produkcji, na moje wyczucie, nowa wersja jest jakieś 30% tańsza. Akurat cena dla klientów IKEA to bardzo istotny czynnik. Nowe łóżko mojej córki dowodzi, że wcale nie musi ucierpieć jakość. Po prostu było pole dla oszczędności w pierwotnej konstrukcji.
#IKEA najwyraźniej sprawdziła, że klientom podoba się ten produkt i zleciła jego przekonstruowanie według wniosków wyciągniętych z doświadczeń użytkowników pierwszej wersji tego łóżka. Nie jest to żaden "Frankenstein" z dodawanymi na szybko zmianami do pierwotnego projektu.
Jest to od początku, gruntownie przemyślany na nowo produkt, nie zmienił się tylko sposób jego używania. Czyli zrobili coś, co wcale nie jest tak częste – zoptymalizowali ten produkt nie tylko w samym procesie produkcji, co jest dobre i powszechne, ale od początku projektując od nowa to łóżko uzyskali niedostępne dla samego Lean Manufacturing korzyści. Najwyraźniej pierwsza wersja była tylko rynkowym sprawdzianem klienckich gustów oraz wyprzedzeniem konkurencji.
Możemy wierzyć, że bardziej zoptymalizować się naszego projektu nie da, tylko jeśli konkurencja w to nie uwierzyła, to może mieć znacznie lepszy produkt. Przy czym lepszy, paradoksalnie może oznaczać gorszej jakości, jeżeli tylko dla klienta jakość nie obniżyła się w ważnych dla niego obszarach.
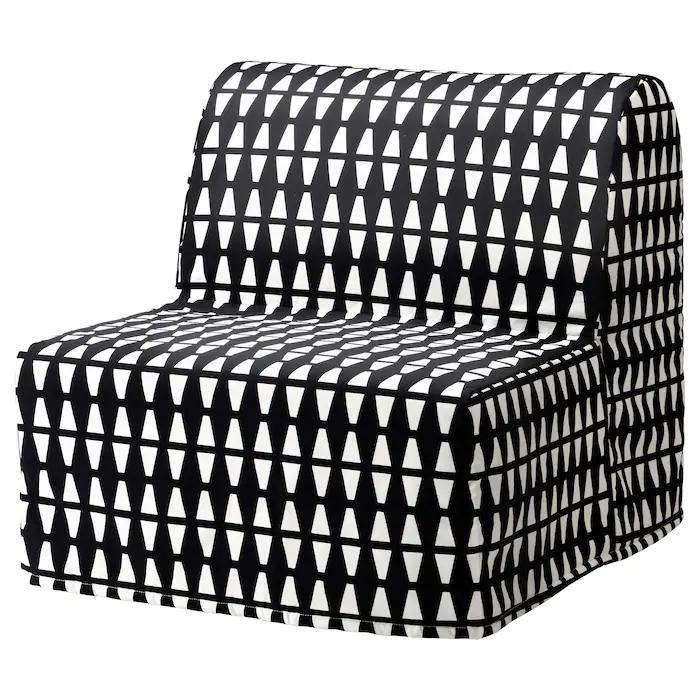
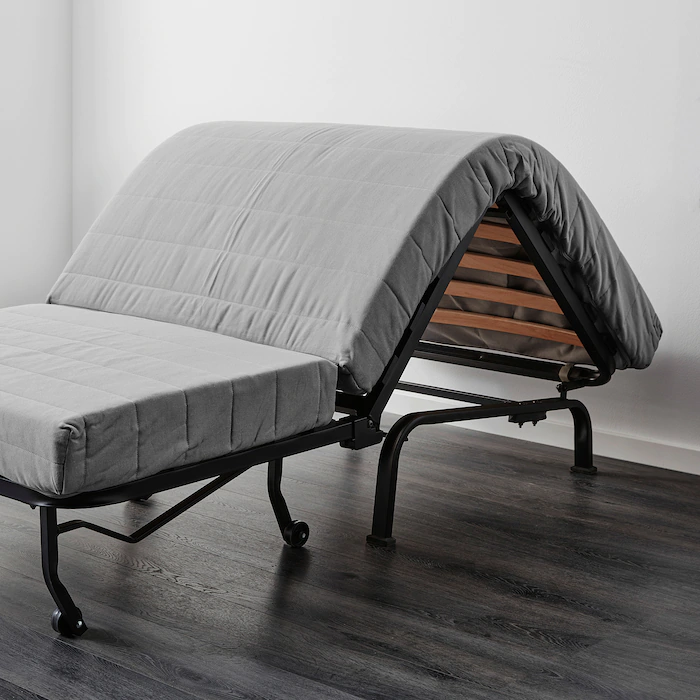
Fot: nowa wersja LYCKSELE LÖVÅS na sesji zdjęciowej, źródło - IKEA
Często modyfikuje się proces produkcyjny tak, aby był jak najbardziej wyszczuplony. Oczywiście należy to robić, jednak managerowie, którzy inwestują środki wyłącznie w Lean Manufacturing nieświadomie pomijają potencjał optymalizacji konstrukcji produktu, szczególnie gdy konstruktorzy dopiero rozpoczeli jego projektowanie.
Czy IKEA nie zapłaciła za proces projektowania dwukrotnie?
Tak, jednak pierwsza konstrukcja powstała szybko i umożliwiła sprawdzenie upodobań rynkowych. Druga nie byłaby konieczna, gdyby okazało się, że produkt nie "chwycił". Na pewno wskazywali tam zmniejszenie ciężaru, bo każdy kilogram mniej do wnoszenia, to bardziej zadowolony klient, a nie tylko oszczędność na produkcji. Poza tym skąd byłoby wiadomo co cenią klienci, gdyby nie badania faktycznych użytkowników pierwszego modelu?
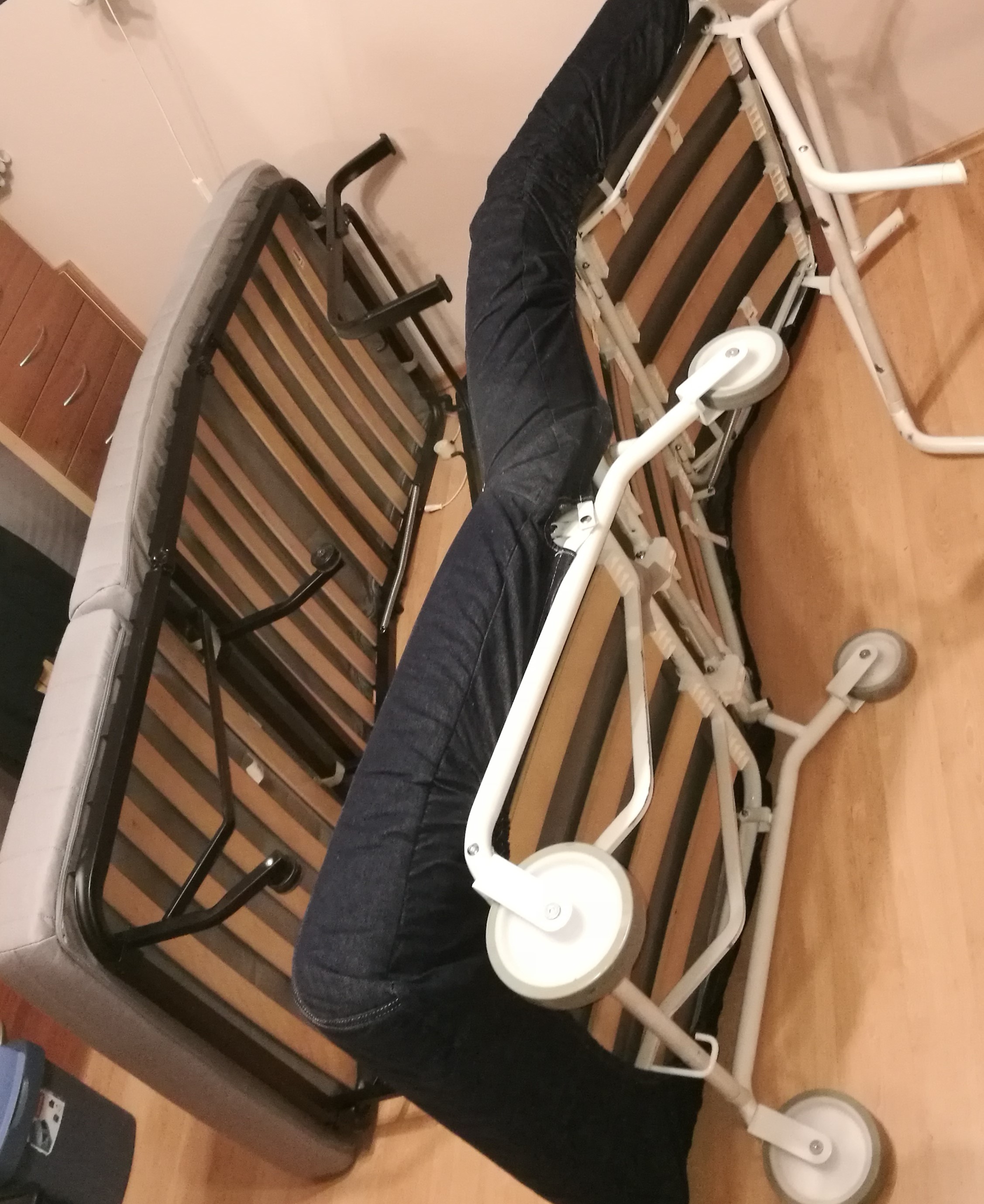
Fot. Porównanie obu wersji, po lewej nowa wersja, po prawej ta mniej optymalna - zdjęcie autora.
Aby była jasność, starsze z tych łóżek też było do pewnego stopnia zoptymalizowane, tylko wizja klienta docelowego była nieco inna. Nawyraźniej kółka miały wjezdzać na masywne dywany. Domyślam się, że później w badaniach użytkowników wyszło, że takich dywanów jest coraz mniej. Niewielki procent użytkowników z dywanem może po prostu nie wybierać tego rozwiązania, uniwersalność jest dobra tylko do pewnego momentu.
Ostatnio udało mi się wywołać małą burzę na LinkedIn wpisem o przyczynach – dlaczego jako inżynierowie zwykle nie optymalizujemy konstrukcji. Jeden z komentujących wskazał, że najpierw inżynier nie oszacowuje dobrze ile mu to zajmie – bo gdyby pokazał prawdziwy szacunek, który pozwalałby mu dobrze zoptymalizować produkt, to nie otrzymałby zlecenia na taką pracę. Potem nie ma czasu na jakąkolwiek optymalizację.
Ale czy koniecznie trzeba robić optymalny projekt od razu, za pierwszym razem?
Czy nie mówiło się kiedyś, żeby zbudować pierwszy dom dla wroga, drugi dla przyjaciela, a dopiero trzeci dla siebie? Inżynier, przy kolejnych iteracjach projektowania i realizowania bardzo dużo może się nauczyć. Ta nauka oprócz kosztów daje też bardzo konkretne zyski na późniejszych etapach życia produktu.
Zgubna może być chęć zrobienia projektu „raz a dobrze” - to odwołanie do zwinnego podejścia zweryfikowanego w software development.
Przyczyn braku optymalizowania jest więcej – brak czasu wcale nie musi wynikać z niedoszacowania czasu na projektowanie. Wystarczy, że klient lub manager przychodzi z bardzo krótkim czasem na zaprojektowanie i jeśli się nie podejmujesz - to podejmie się ktoś inny. Tu przydałaby się umiejętność argumentowania, by wytłumaczyć realne opcje komuś, kto nie jest inżynierem. Zwykle właśnie tej umiejętności inżynierom brakuje. Managerowie widzą tylko duże ryzyko i gdy nie zauważają możliwych korzyści, to optymalizacji nie będzie.
Są jednak też mniej oczywiste powody, dla których nie optymalizujemy swoich konstrukcji. Jedna z nich to obawy inżyniera - często zamiast wsparcia u swojego managera, który nie rozumie zamysłu technicznego, konstruktor odczuwa zbyt duże ryzyko porażki. Sam często nie potrafi przekonać zarządzających do drążenia dalej ulepszania. Gdy brakuje mu pewności siebie, to woli nie podejmować zbyt ryzykownych działań - to jest bezpieczniejsze. Niestety w dłuższej perspektywie zbytnie asekuranctwo może mieć złe skutki. Świadczą o tym od lat nie optymalizowane konstukcje w wielu firmach. Wniosek z tego taki - inżynierowie jak wszyscy ludzie, potrzebują w sytuacji niepewności wsparcia od innych, szczególnie managerów.
Nie wszyscy mają też prawdziwe umiejętności w dziedzinie optymalizacji, ktoś kto nie odchudził wielu konstrukcji, bo ciągle nie było na to czasu, raczej nie osiągnie takiego efektu jak ten, kto od wielu lat właśnie głównie optymalizował projekty. Zwykle po drodze tego bardziej doświadczonego w "odchudzaniu" inżyniera były też szkolenia z Design for Assembly, Design for Manufacturing czy TRIZ Trimming.
Inną przyczyną jest brak świadomości kiedy skończyć "ulepszanie". Z jednej strony skoro dobry prototyp działa, to lepiej go zostawić, aby nic nie zepsuć. Z drugiej strony boimy się, że konkurencja nas wyprzedzi, kiedy czekamy na poprawki. Trzecie podejście bierze zalety z dwóch poprzednich i idzie dalej. To kilka iteracji projektu - konstruowania od nowa. Wówczas jesteśmy wcześnie na rynku z pierwszą, szybką, lecz niedopracowaną koncepcją. Kolejne wersje będą lepsze również dla tego, że wzieliśmy pod uwagę doświadczenia użytkowników z wcześniejszych projektów, ich opinie zawsze zaskakują i prowadzą do lepszych rozwiązań.
Pamiętać przy tym trzeba o efekcie skali. IKEA operuje milionami sztuk swoich produktów, koszt powtórnego projektowania podzielony na takie ilości szybko się zwraca. Znam jednak przykłady opłacalności stosowania DFA w produkcji małoseryjnej. Czy to prawda, że obecnie koszty montażu rosną szybciej niż koszty projektowania wspieranego przez kolejne narzędzia?
Powodów jest oczywiście jeszcze więcej, na przykład przywiązanie do własnych pomysłów. Pomysłów, które kosztowały nas sporo wysiłku i prób. Psychologowie zbadali, że pomysły okupione dużym wysiłkiem są przez autorów wyceniane o wiele, wiele wyżej niż widzą to osoby postronne. Nazywa się to afektem ojcowskim. Gdy przychodzi inny inżynier bez takiego emocjonalnego związku z projektem, to szybko zauważa możliwości i proponuje uproszczenia. „Ojciec” oryginalnego projektu musi zaś mocno się ugiąć do ulepszania swojego „dziecka”. Szczególnie jeśli był bardzo z niego dumny. Choć oczywiście nie brakuje takich, którzy sami bez końca by dopieszczali i nigdy nie uważają swojego dzieła za dokończone. Dla nich dobrą opcją może być podejście z software - kilka iteracji z wersją Alpha, Beta itd.
Chyba ostatnia sprawa to ciągle zmieniające się gusta, mody i okoliczności. Chyba nie będzie jedynej wiecznej i na zawsze ostatecznej wersji czegokolwiek, co projektują inżynierowie (choć w budownictwie można się do tego zbliżyć). Dlatego warto co jakiś czas odświeżać swoje projekty. Trzeba tylko do takich inwestycji w nową konstrukcję przekonać managerów/finansistów. To z tego powodu robimy szkolenia dla inżynierów ze sztuki argumentowania i przekonywania.
W Polsce jest niewiele firm tak optymalizujących swoje konktrukcje jak IKEA. Dzięki szkoleniom dla inżynierów poznałem już jednak takich konstruktorów, którzy od niedawna potrafią za pierwszym razem zrobić od razu zoptymalizowaną wg. DFA konstrukcję. Jest to jednak w mojej ocenie tylko promil wszystkich firm w naszym kraju, w których pracują konstruktorzy.
To jest opinia Michała Hałasa
możesz się z nią niezgodzić - odpisz co poprawić. Michał pracuje jeszcze nad redukcją swojego afektu ojcowskiego względem tego tekstu.